The 9-Minute Rule for Premier Aluminum Llc
The 9-Minute Rule for Premier Aluminum Llc
Blog Article
The Premier Aluminum Llc PDFs
Table of ContentsFacts About Premier Aluminum Llc RevealedPremier Aluminum Llc Fundamentals ExplainedThe Greatest Guide To Premier Aluminum LlcThe Only Guide for Premier Aluminum Llc
(https://wi-racine.cataloxy.us/firms/www.premieraluminum.com.htm)Utilizing reduced price and unqualified vendors can cause quality problems, and lost time and cash in the lengthy run. To aid you with the procedure, right here are some points to think about when choosing the best metal casting supplier.
A company that only utilizes the financial investment casting process will attempt to offer you on why that procedure is best for your application (Foundries in Wisconsin). But what happens if using the sand casting procedure is best for you and your requirements? Instead, try to find a vendor that uses a series of casting processes so the ideal option for YOU is selected
If dealing with a single source for every one of your casting needs is necessary to you, the distributor needs to be diverse in its capacities. When integrated with other integrated capabilities, this can help simplify and compress the supply base. When choosing the best spreading supplier, mindful factor to consider ought to be provided to quality, solution, and cost.
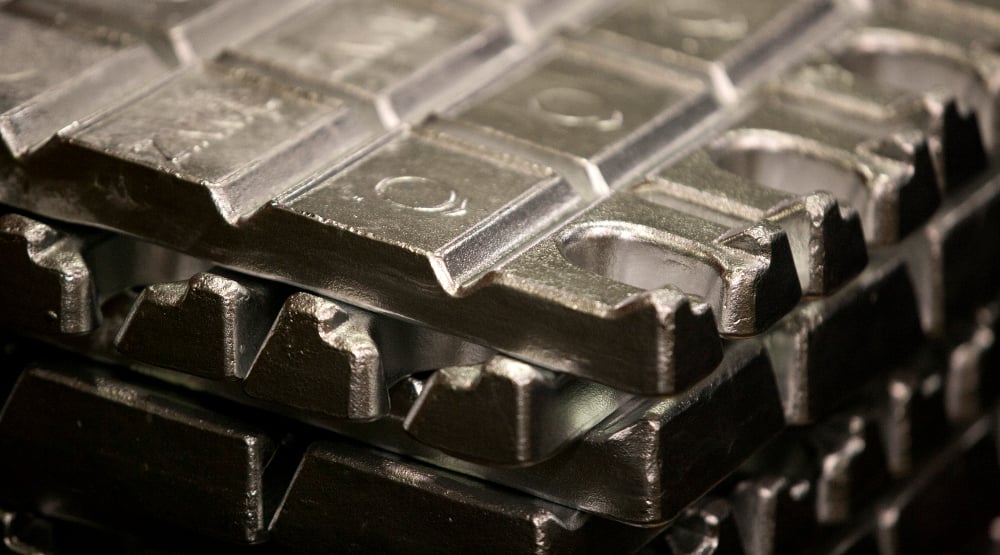
Some Known Questions About Premier Aluminum Llc.
Customers increasingly select casting suppliers who have machining abilities. If the spreading distributor finds an issue during machining, the problem is solved much faster with no conflict over whose fault it is.
Trouble or no, integrated machining streamlines the supply chain and decreases dealing with time and delivery cost prior to the item makes it to the client. What do you need from your spreading vendor? Are you trying to find somebody to just provide a steel part to your doorstep or do you require a lot more? If you do not have in-house metallurgy know-how, confirm that the distributor can provide assistance in selecting the proper alloy based on your particular application.
Some shops are limited or specialized. Make sure the provider can satisfy all your product or alloy needs to get rid of the demand for numerous providers.
How Premier Aluminum Llc can Save You Time, Stress, and Money.
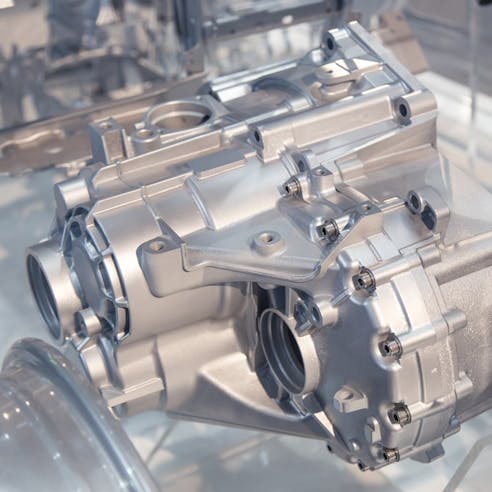
Research study the supplier's web site. Talk to a sales associate or service associate.
Light weight aluminum is likewise light-weight and has excellent corrosion resistance, making it excellent for applications where weight and longevity are crucial variables. Additionally, light weight aluminum casting is an economical approach of production, as it needs much less power and sources than various other approaches. Iron spreading, on the other hand, includes pouring liquified iron into a mold and mildew to create a desired shape.
Little Known Questions About Premier Aluminum Llc.
Iron spreading is likewise able to stand up to high temperatures, making it appropriate for usage in applications such as engine parts and commercial machinery. Iron casting can be more costly than light weight aluminum spreading due to the higher expense of raw materials and the power required to melt the iron. When deciding in between light weight aluminum casting and iron spreading, it is essential to think about the details needs of the application.
If strength and sturdiness are more vital, iron spreading may be the far better choice. Other factors to take into consideration include price, production volume, and preparation. To conclude, both light weight aluminum casting and iron spreading have their very own special advantages and drawbacks. By very carefully thinking about the details needs of the application, makers can select the ideal find more info process for their product.ZheJiang Dongrun Spreading Sector Carbon Monoxide,. Ltd was constructed in 1995, We have actually remained in the spreading market for greater than 25 years. Die casting is the name offered to the
process of creating complex metal components with use molds of the element, also referred to as dies. The procedure utilizes non-ferrous metals which do not have iron, such as light weight aluminum, zinc and magnesium, as a result of the preferable residential or commercial properties of the metals such as low weight, greater conductivity, non-magnetic conductivity and resistance to rust. Die casting manufacturing is quickly, making high manufacturing levels of components very easy.
It creates more parts than any type of other procedure, with a high level of accuracy and repeatability. To get more information concerning die casting and pass away spreading materials made use of at the same time, reviewed on. There are 3 sub-processes that fall under the classification of die casting: gravity pass away spreading (or irreversible mold casting), low-pressure die spreading and high-pressure die casting. The pure metal, also referred to as ingot, is included in the heater and maintained the molten temperature level of the steel, which is after that movedto the injection chamber and infused right into the die. The pressure is after that preserved as the steel solidifies. As soon as the metal strengthens, the cooling procedure begins. The thicker the wall surface of the part, the longer the cooling time due to the quantity of indoor metalthat additionally needs to cool. After the element is totally cooled, the die cuts in half open and an ejection mechanism presses the part out. Complying with the ejection, the die is shut for the next injection cycle. The flash is the added product that is cast throughout the process. This must be cut off utilizing a trim tool to
leave just the major component. Deburring removes the smaller pieces, called burrs, after the trimming procedure. Finally, the part is polished, or burnished, to provide it a smooth coating. This verified to be an incorrect examination, since the tester could reduce into an item and miss an area with porosity. Today, top suppliers use x-ray screening to see the whole inside of parts without reducing right into them. This enables them to much more accurately approve or reject parts. To get to the finished product, there are 3 key alloys utilized as die spreading material to pick from: zinc, light weight aluminum and magnesium. Zinc is among the most previously owned alloys for die spreading due to its lower expense of resources. Report this page